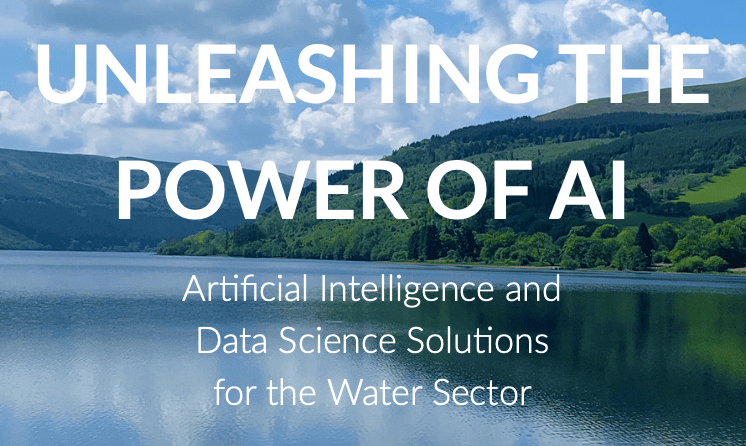
- INTELLIGENCE
- …
- INTELLIGENCE
- INTELLIGENCE
- …
- INTELLIGENCE
CASE STUDIES
Optimising water treatment
in the Netherlands
A water utility based in Northern Holland were seeking to optimize the use of expensive chemical in the water treatment process at one of their key water treatment facilities. They needed to ensure water output could be maintained despite variable incoming water quality from two sources.
What was the need?
They were under pressure to reduce their costs and their carbon footprint. Small over-dosing of coagulant, marginal energy inefficiencies from pumping and rapid clogging of filters were all believed to be driving down the overall efficiency of the plant. Despite a highly skilled team operating the facility, it was expected there were operational efficiencies that could be achieved with a systematic approach to optimization.
The challenge
In particular they wanted to optimize the use of chemical coagulants. The water they were treating had variable turbidity and required more coagulant when the turbidity was higher. The efficacy of the coagulant varies based on the temperature of the water, and the efficacy of the coagulation step had an impact on how well the sand filters further downstream were performing. They were regularly faced with the question: should we increase coagulant dosing – using expensive chemicals – and reduce the burden on the sand filters? or can we reduce the chemical dosing and still achieve the desired quantity of water through the plant.
What did the AI model do?
In this solution the measured relationship between temperature, coagulant efficacy and turbidity at the site was modelled so that the effect of the coagulation process could be predicted. In this way precisely the right amount of coagulant could be added, making sure that the downstream processes were not negatively affected, and water treatment parameters were always met. The variation in natural turbidity was modelled from the raw water, and the whole throughput of the plant was modelled so that quantity of water required from the plant could be part of the prediction.
The outcome
A decision support system that can account for a wide set of variables in real-time, ensuring that the right decisions are made concerning the water treatment process steps. The plant’s processes are now deemed to be ‘optimal’, which equates to an underlying efficiency improvement estimated at 10%. Target water treatment outputs can now be maintained through periods of variable incoming water quality.
To find out more about how Collaborate Water can use the power of your data to transform your operations:
Email us: info@collaboratewater.com
Sign up for our newsletter:
© Copyright-2023 Collaborate Water - Privacy Policy